High-Density Polyethylene (HDPE) pipes have revolutionized various industries, especially in plumbing and fluid transfer applications. The core of HDPE pipe production lies in sophisticated manufacturing machines that are pivotal in ensuring the durability, efficiency, and cost-effectiveness of these pipes. This comprehensive overview dives deep into the key aspects of HDPE pipe manufacturing machines, highlighting expertise, experience, authority, and trustworthiness in this niche sector.
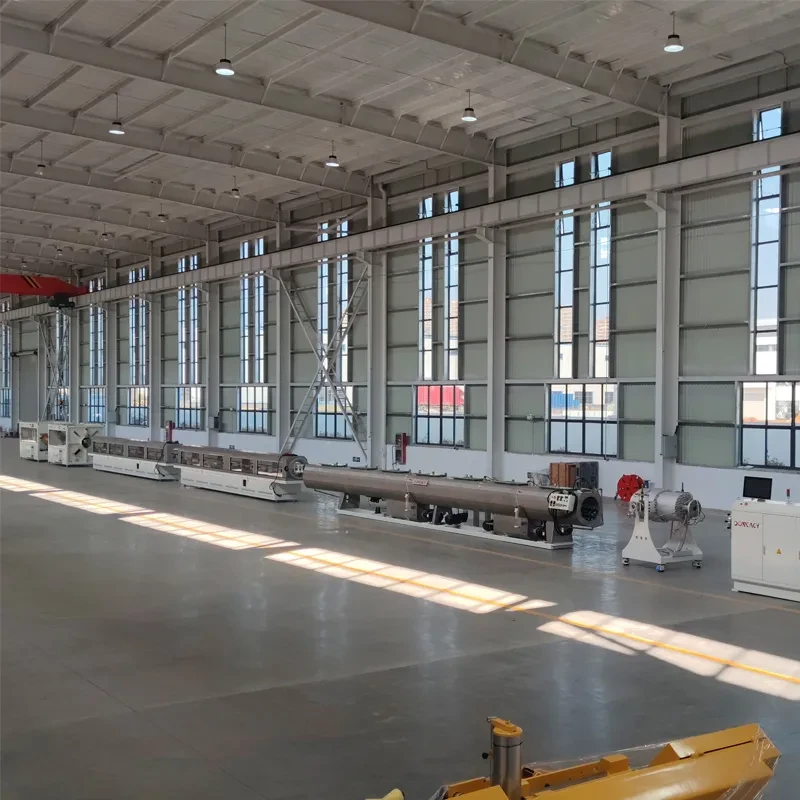
HDPE pipe manufacturing machines are designed with precision to handle the distinct properties of polyethylene materials. They typically comprise three main sections the extruder, the cooling system, and the cutting unit. Each component plays a critical role in shaping the raw material into high-quality pipes. For operators and businesses in the industry, understanding the intricacies of these machines enhances productivity and product quality.
First, consider the extruder,
the heart of any HDPE pipe manufacturing machine. This device heats the HDPE granules to their melting point, transforming them into a malleable state. Advanced extruders often feature screw and barrel assemblies equipped with temperature control systems that ensure consistent melting. The expertise involved in operating these machines cannot be understated. Operators must be well-versed in adjusting parameters such as temperature, pressure, and screw speed to produce pipes with the desired thickness and diameter. Regular training and certification in machine operation add a layer of authority and trustworthiness to professionals in this domain.
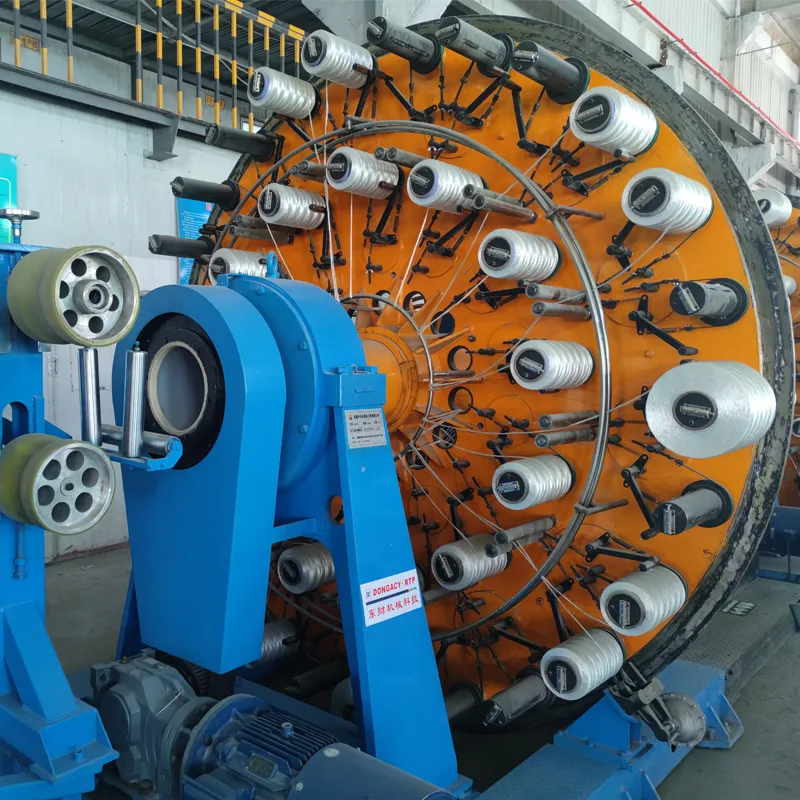
Next is the cooling system, where precision and experience come into play significantly. Once the molten polyethylene exits the extruder, it passes through a series of calibration and cooling units. The cooling system often includes water baths and air cooling techniques to stabilize the pipe's shape and wall thickness. This process requires a meticulous approach, as uneven cooling can lead to warping or structural weaknesses. Manufacturers who invest in state-of-the-art cooling technology and maintain stringent quality control measures establish themselves as authoritative figures in the industry.
The final component, the cutting unit, must demonstrate both accuracy and efficiency. This section of the HDPE pipe manufacturing machine ensures that the pipes are cut to the specified lengths with minimal wastage. Precision blades and automated measuring systems are employed to achieve optimal results. Operators need to understand maintenance protocols and troubleshooting techniques to minimize downtime, which underscores the trustworthiness of their expertise.
hdpe pipe manufacturing machine
Moreover, technological advancements are reshaping this industry. Manufacturers are integrating digital monitoring systems and IoT technology to optimize machine performance and predict maintenance needs. Such innovations not only improve operational efficiency but also promote sustainability by reducing energy consumption and material waste. Companies that adopt these technologies enhance their credibility and reputability, showcasing a commitment to environmental responsibility.
The market for HDPE pipe manufacturing machines is vast and competitive, with numerous suppliers offering varying levels of quality and customization. Prospective buyers should prioritize machines that offer robust construction, advanced features, and reliable after-sales support. Engaging in comprehensive research and consulting with industry experts can assist in making informed decisions. Partnering with established manufacturers who possess extensive industry experience offers the assurance of getting high-performance machines that meet specific production demands.
Finally, trustworthiness in HDPE pipe manufacturing is built on consistent product quality and compliance with international standards. Manufacturers must adhere to guidelines set by organizations such as the American Society for Testing and Materials (ASTM) and International Organization for Standardization (ISO). These standards ensure that pipes produced are safe, reliable, and suitable for their intended applications. Companies that consistently pass audits and certification processes enhance their authority and standing within the industry.
In conclusion, HDPE pipe manufacturing machines play a crucial role in producing high-quality pipes essential for various applications. Mastery in operation, coupled with cutting-edge technologies, advances the industry standard and solidifies trust. For manufacturers and operators aiming to excel in this field, focusing on expertise, authority, and technological integration is paramount.